КАТЕГОРИИ:
Архитектура-(3434)Астрономия-(809)Биология-(7483)Биотехнологии-(1457)Военное дело-(14632)Высокие технологии-(1363)География-(913)Геология-(1438)Государство-(451)Демография-(1065)Дом-(47672)Журналистика и СМИ-(912)Изобретательство-(14524)Иностранные языки-(4268)Информатика-(17799)Искусство-(1338)История-(13644)Компьютеры-(11121)Косметика-(55)Кулинария-(373)Культура-(8427)Лингвистика-(374)Литература-(1642)Маркетинг-(23702)Математика-(16968)Машиностроение-(1700)Медицина-(12668)Менеджмент-(24684)Механика-(15423)Науковедение-(506)Образование-(11852)Охрана труда-(3308)Педагогика-(5571)Полиграфия-(1312)Политика-(7869)Право-(5454)Приборостроение-(1369)Программирование-(2801)Производство-(97182)Промышленность-(8706)Психология-(18388)Религия-(3217)Связь-(10668)Сельское хозяйство-(299)Социология-(6455)Спорт-(42831)Строительство-(4793)Торговля-(5050)Транспорт-(2929)Туризм-(1568)Физика-(3942)Философия-(17015)Финансы-(26596)Химия-(22929)Экология-(12095)Экономика-(9961)Электроника-(8441)Электротехника-(4623)Энергетика-(12629)Юриспруденция-(1492)Ядерная техника-(1748)
|
Види дефектів в процесі виготовлення гумотехнічних виробів
ДОДАТОК С
Схеми технологічних процесів
ДОДАТОК Р
План виробничого приміщення
ДОДАТОК П
Властивості насиченої водяної пари в залежності від тиску
Властивості насиченої водяної пари в залежності від температури
ДОДАТОК О
Температура 0С
| Тиск абсолютний, кгс/с2
| Питомий об’єм, м3/кг
| Густина кг/м3
| Питома ентальпія рідини, кДж/кг
| Питома ентальпія пари, кДж/кг
| Питома теплота пароутво-рення, кДж/кг
| | Р
| ν
| ρ
| ік
| in
| г
|
| 0,0062
| 206,5
| 0,00484
|
| 2493,1
| 2493,1
|
| 0,0089
| 147,1
| 0,00680
| 20,95
| 2502,7
| 2481,7
|
| 0,0125
| 106,4
| 0,00940
| 41,90
| 2512,3
| 2470,4
|
| 0,0174
| 77,9
| 0,01283
| 62,85
| 2522,4
| 2459,5
|
| 0,0238
| 57,8
| 0,01729
| 83,800
| 2532,0
| 2448,2
|
| 0,0323
| 43,40
| 0,02304
| 104,75
| 2541,7
| 2436,9
|
| 0,0433
| 32,93
| 0,03036
| 125,70
| 2551,3
| 2425,6
|
| 0,0573
| 25,25
| 0,03960
| 146,65
| 2561,0
| 2414,3
|
| 0,0752
| 19,55
| 0,05114
| 167,60
| 2570,6
| 2403,0
|
| 0,0977
| 15,28
| 0,06543
| 188,55
| 2579,8
| 2391,3
|
| 0,1258
| 12,054
| 0,0830
| 209,50
| 2589,5
| 2380,0
|
| 0,1605
| 9,589
| 0,1043
| 230,45
| 2598,7
| 2368,2
|
| 0,2031
| 7,687
| 0,1301
| 251,40
| 2608,3
| 2356,9
|
| 0,2550
| 6,209
| 0,1611
| 272,35
| 2617,5
| 2345,2
|
| 0,3177
| 5,052
| 0,1979
| 293,30
| 2626,3
| 2333,0
|
| 0,393
| 4,139
| 0,2416
| 314,3
|
|
|
| 0,483
| 3,414
| 0,2929
| 335,2
|
|
|
| 0,590
| 2,832
| 0,3531
| 356,2
|
|
|
| 0,715
| 2,365
| 0,4229
| 377,1
|
|
|
| 0,862
| 1,985
| 0,5039
| 398,1
|
|
|
| 1,033
| 1,675
| 0,5970
| 419,0
|
|
|
| 1,232
| 1,421
| 0,7036
| 440,4
|
|
|
| 1,461
| 1,212
| 0,8254
| 461,3
|
|
|
| 1,724
| 1,038
| 0,9635
| 482,7
|
|
|
| 2,025
| 0,893
| 1,1199
| 504,1
|
|
|
| 2,367
| 0,7715
| 1,296
| 555,4
|
|
|
| 2,755
| 0,6693
| 1,494
| 546,8
|
|
|
| 3,192
| 0,5831
| 1,715
| 568,2
|
|
|
| 3,685
| 0,5096
| 1,962
| 589,5
|
|
|
| 4,238
| 0,4469
| 2,238
| 611,3
|
|
|
| 4,855
| 0,3933
| 2,543
| 632,7
|
|
|
| 6,303
| 0,3075
| 3,252
| 654,1
|
|
|
| 8,080
| 0,2431
| 4,113
| 719,8
|
|
|
| 10,23
| 0,1944
| 5,145
| 763,8
|
|
|
| 12,80
| 0,1568
| 6,378
| 808,3
|
|
|
| 15,85
| 0,1276
| 7,840
| 852,7
|
|
|
| 19,55
| 0,1045
| 9,567
| 897,9
|
|
|
| 23,66
| 0,0862
| 11,60
| 943,2
|
|
|
| 28,53
| 0,7155
| 13,98
| 988,3
|
|
|
| 34,13
| 0,05967
| 16,76
|
|
|
|
| 40,55
| 0,04998
| 20,01
|
|
|
|
| 47,85
| 0,04199
| 23,82
|
|
|
|
| 56,11
| 0,03538
| 28,27
|
|
|
|
| 65,42
| 0,02988
| 33,47
|
|
|
|
| 75,88
| 0,02525
| 39,60
|
|
|
|
| 87,6
| 0,02131
| 46,93
|
|
|
|
| 100,7
| 0,01799
| 55,59
|
|
|
|
| 115,2
| 0,01516
| 65,95
|
|
|
|
| 131,3
| 0,01273
| 78,53
|
|
|
|
| 149,0
| 0,01064
| 93,98
|
|
|
|
| 168,6
| 0,00884
| 113,2
|
|
|
|
| 190,3
| 0,00716
| 139,6
|
|
| 713,6
|
| 214,5
| 0,00585
| 171,0
|
|
| 411,5
|
|
| 0,00310
| 322,6
|
|
|
|
Температура 0С
| Тиск абсолютний, кгс/с2
| Питомий об’єм, м3/кг
| Густина кг/м3
| Питома ентальпія рідини, кДж/кг
| Питома ентальпія пари, кДж/кг
| Питома теплота пароутворення, кДж/кг
| | Р
| ν
| ρ
| ік
| in
| г
| 6,6
| 0,01
| 131,60
| 0,00760
| 27,7
|
|
| 12,7
| 0,015
| 89,64
| 0,01116
| 53,2
|
|
| 17,1
| 0,02
| 68,27
| 0,01465
| 71,6
|
|
| 20,7
| 0,025
| 55,28
| 0,01809
| 86,7
|
|
|
| 0,03
| 46,53
| 0,02149
| 99,3
|
|
| 28,6
| 0,04
| 35,46
| 0,02820
| 119,8
|
|
| 32,5
| 0,05
| 28,73
| 0,03481
| 136,2
|
|
| 35,8
| 0,06
| 24,19
| 0,04133
| 150,0
|
|
| 41,1
| 0,08
| 18,45
| 0,05420
| 172,2
|
|
| 45,4
| 0,10
| 14,96
| 0,06686
| 190,2
|
|
| 49,0
| 0,12
| 12,60
| 0,07937
| 205,3
|
|
| 53,6
| 0,15
| 10,22
| 0,09786
| 224,6
|
|
| 59,7
| 0,20
| 7,977
| 0,1283
| 250,1
|
|
| 68,7
| 0,30
| 5,331
| 0,1876
| 287,9
|
|
| 75,4
| 0,40
| 4,072
| 0,2456
| 315,9
|
|
| 80,9
| 0,50
| 3,304
| 0,3027
| 339,0
|
|
| 85,5
| 0,60
| 2,785
| 0,3590
| 358,2
|
|
| 89,3
| 0,70
| 2,411
| 0,4147
| 375,0
|
|
| 93,0
| 0,80
| 2,128
| 0,4699
| 389,7
|
|
| 96,2
| 0,90
| 1,906
| 0,5246
| 403,1
|
|
| 99,1
| 1,0
| 1,727
| 0,5790
| 415,2
|
|
| 104,2
| 1,2
| 1,457
| 0,6865
| 437,0
|
|
| 108,7
| 1,4
| 1,261
| 0,7931
| 456,3
|
|
| 112,7
| 1,6
| 1,113
| 0,898
| 473,1
|
|
| 116,3
| 1,8
| 0,997
| 1,003
| 483,6
|
|
| 119,6
| 2,0
| 0,903
| 0,107
| 502,4
|
|
| 132,9
| 3,0
| 0,6180
| 0,618
| 558,9
|
|
| 142,9
| 4,0
| 0,4718
| 2,120
| 601,1
|
|
| 151,1
| 5,0
| 0,3825
| 2,614
| 637,7
|
|
| 158,1
| 6,0
| 0,3222
| 3,104
| 667,9
|
|
| 164,2
| 7,0
| 0,2785
| 3,591
| 694,3
|
|
| 169,6
| 8,0
| 0,2454
| 4,075
| 718,4
|
|
| 174,5
| 9,0
| 0,2195
| 4,536
| 740,0
|
|
| 179,0
|
| 0,1985
| 5,037
| 759,6
| 27,84
|
| 183,2
|
| 0,1813
| 5,516
| 778,1
|
|
| 187,1
|
| 0,1668
| 5,996
| 795,3
|
|
| 190,7
|
| 0,1545
| 6,474
| 811,2
|
|
| 194,1
|
| 0,1438
| 6,952
| 826,7
|
|
| 197,4
|
| 0,1346
| 7,431
| 840,9
|
|
| 200,4
|
| 0,1264
| 7,909
| 854,8
|
|
| 203,4
|
| 0,1192
| 8,389
| 867,7
|
|
| 206,2
|
| 0,1128
| 8,868
| 880,3
|
|
| 208,8
|
| 0,1070
| 9,349
| 892,5
|
|
| 211,4
|
| 0,1017
| 9,83
| 904,2
|
|
| 232,8
|
| 0,06802
| 14,70
|
|
|
| 249,2
|
| 0,05069
| 19,73
|
|
|
| 262,7
|
| 0,04007
| 24,96
|
|
|
| 274,3
|
| 0,03289
| 30,41
|
|
|
| 284,5
|
| 0,02769
| 36,12
|
|
|
| 2983,6
|
| 0,02374
| 42,13
|
|
|
| 301,9
|
| 0,02064
| 48,45
|
|
|
| 309,5
|
| 0,01815
| 55,11
|
|
|
| 323,1
|
| 0,01437
| 69,60
|
| 26,38
|
| 335,0
|
| 0,01164
| 85,91
|
|
|
| 345,7
|
| 0,00956
| 104,6
|
|
|
| 355,4
|
| 0,00782
| 128,0
|
|
|
| 364,2
|
| 0,00614
| 162,9
|
|
|
| 374,0
|
| 0,00310
| 322,6
|
|
|
|
Сітку колон приміщення виконують розмірами: 6х18, 12х18, 12х24.
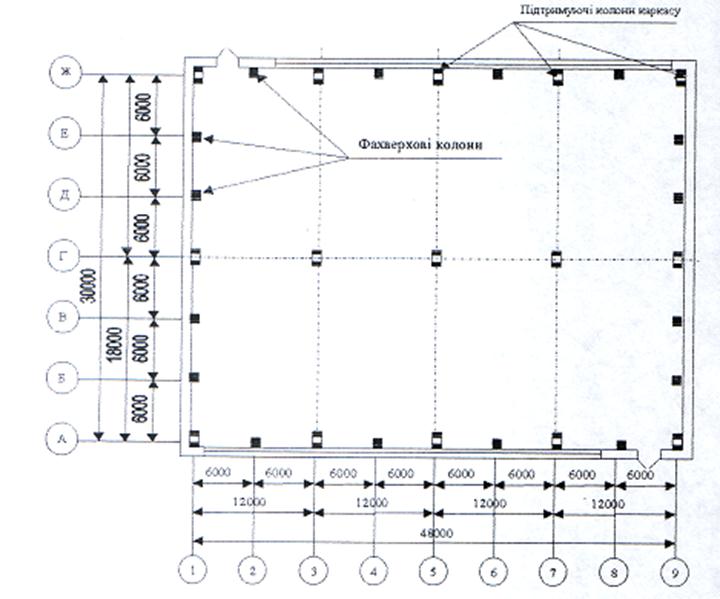
Колони виконують одно і двохвіткові
Розміри колон у розрізі, мм:
одновіткові: 400х400, 500х500, 400х600
двохвіткові: 400х800, 400х1000, 600х1900.
Фахверхові колони (для підтримки стінових панелей) мають розміри, мм: 300х300, 400х600.
Виробництво обгумованих валів
Таблиця 1 - Види дефектів, методи їх попередження
Види дефектів
| Метод контролю
| Метод попередження
| 1. Повітряні
міхури
| Візуально
| Проколювання повітряних міхурів голкою перед бинтуванням, ретельне бинтування
| 2. Відшарову-
вання
| Простукування молотком
| Якісне чищення і промазка металу, дотримання термінів зберігання розігрітої гумової суміші і каландрованого полотна
| 3. Невідповід-
ність
твердості
обкладки
| Вимірювання твердості кульковим твердоміром
| Дотримання рецептури
| 4. Невідповід-
ність
розмірів
| Замір рулеткою
| Обробка валу згідно розмірів, вказаним на кресленнях
| 5. Включення
сторонніх
предметів
| Візуально
| Підтримувати в чистоті робоче місце
|
Виробництво формових виробів методом лиття під тиском
Таблиця 2 - Види браку, причини виникнення, методи усунення
Види дефектів
| Причини виникнення
| Методи усунення
| 1. Пухирі усередині деталі, є пустоти
| Захват повітря при наборі гумової суміші в литтєву камеру. Наяв-ність повітря в гумовій суміші. Підвищена вогкість інгредієнтів
| Збільшити протитиск. Знизити температуру суміші в литтєвій камері.
Не застосовувати вологі інгредієнти
| 2. Сторонні включення і включення підвулканізо-ваної гуми
| Попадання в суміш сторонніх включень, наявність залишків гуми на поверхні прес-форми і літнику
| Виключити попадання сторонніх включень в гумову суміш. Ретельно очищати прес-форму при її перезарядці
| 3. Недовул-канізовані деталі
| Недостатня ступінь вулканізації
| Підвищити температуру прес-форми або тривалість вулка-нізації, підвищити температуру суміші в литтєвому каналі. Збільшити тривалість вулканізації
| 4. Недолив, часткове недооформ-лення деталі
| Недостатня доза вприску та тиск вприску.
Підвулканізація гумової суміші
| Збільшити дозу вприску, уточнити розмір гумової стрічки. Збільшити тиск вприску, знизити температуру прес-форми. Перевірити гумову суміш на ступінь підвулканізації
| 5. Розшаруван-ня, невеликі тріщини по поверхні деталі
| Підвулканізація гумової суміші, різниця температури плит
| Знизити температуру вулканізації, перевірити температуру плит
|
6. Пористість всієї деталі | Неоптимальний режим вулканізації. Недостатній тиск стулення прес-форми
| Збільшити температуру або тривалість вулканізації. Переві-рити і відрегулювати тиск сту-лення прес-форми. Перевірити вміст летючих речовин
| 7. Підгорілі вироби, відхилення від розмірів деталей
| Висока температура вулканізації. Нерівномірна усадка деталей при вулканізації
| Знизити температуру прес-форми. Перевірити в'язкість гумової суміші
|
Виробництво рукавів бездорновим методом
Таблиця 3 - Види дефектів, причини виникнення і заходи по їх попередженню
Види дефектів
| Причини виникнення
| Заходи по попередженню
|
1. Невідповідність внутрішнього та зовнішнього діаметру | Неправильна товщина гумових шарів. Порушення конструкції рукава
| Перевіряти товщину гумових шарів. Дотримуватися техно-логічного регламенту
| 2. Сторонні включення
| Забруднення робочого місця при виготовленні гумової суміші. Погане перемішування
| Тримати в чистоті робоче місце
Ретельно перемішувати суміш
| 3. Розшарування, пористість зовнішнього гумового шару
| Погане просушування промазаних клеєм шарів
| Убирати надлишки клею, ретельно просушувати камеру
| 4. Складки по всьому рукаві
| Широка камера.
Вільна клейка
| Перевіряти розміри камери
Слідкувати за якістю склеювання
| 5. Різнотовщинність стінок
| Великий нахльост. Розташування нахльосту на одній стороні рукава і широкій камері
| Перевіряти товщину гумового шару. Розташовувати нахлести по всьому рукаву
| 6. Спотворення перетину рукава
| Великий натяг при укладці вулканізованих рукавів на барабан
| Не допускати великого на тяжіння при укладці вулканізованих рукавів на барабан
| 7. Різноколір по зовнішньому шару рукавів
| Збільшення адгезійних властивостей гумової суміші
| Не перевищувати адгезійні властивості гумових сумішей
|
Виробництво регенерату
Таблиця 4 - Види браку, причини виникнення і заходи по попередженню
Найменування браку
| Причини виникнення
| Заходи по попередженню
| 1. Підвищений вміст летючих речовин
| Підвищений вміст вологи в регенераті
| Дотримання технологічних параметрів на девулканізаторі, не допускати у виробництво пом’якшувальний засіб з великим вмістом вологи
| 2. Підвищений вміст золи
| Використовування брудних зношених покришок
| Проводити миття зношених покришок
| 3. Підвищений вміст металевих
включень
| Погано працює елек-тромагніт, застосо-вуються покришки з металокордом
| Не допускати у виробництво покришки з металокордом, стежити за роботою електромагніту
| 4. Підвищений вміст нерозвальцьо-ваних частинок
| Невідповідність розміру сітки, наяв-ність поривів в сітці
| Не допускати установку сіток порваних або не відповідних розміру
|
Виробництво клинових пасів
Таблиця 5 - Види дефектів, причини виникнення і міри по їх попередженню
Види дефектів
| Причини виникнення
| Заходи по попередженню
| 1. Недопресовка
| Знижена маса заготівки, занижений тиск пресування
| Суворо дотримувати масу заготівок пасів при збірці. Суворо дотримувати встановлений тиск пресування
| 2. Здири, розриви
| Брудна прес-форма
| Регулярно проводити чищення прес-форм
| 3. Косі і перевернені паси
| Усадка кордшнура, неправильне розташування паса в канавках прес-форми
| Суворо дотримувати режим просочення кордшнура. Правильно закладати паси в канавки прес-форми
| 4. Розбіжність швів, складки, закус на пасах
| Недбала обгортка клинових пасів. Невідповідність ширини обгортувальної стрічки
| Якісно проводити обгортку клинових пасів. Суворо витримувати ширину обгортувальної стрічки
| 5. Заусенці
| Недбала обгортка осердя. Недотримання маси, висоти заготівок осердя
| Якісно здійснювати обгортку осердя. Контролювати масу і висоту заготівок
| 6. Довгі або короткі паси
| Брак прес-форми по довжині кола
| Виключити застосування форм з відхиленнями по довжині
|
Виробництво формових виробів компресійним методом
Таблиця 6 - Види браку, причини виникнення, методи усунення
Види дефектів
| Причини виникнення
| Методи усунення
| 1. Недопресовка
| Зниження тиску
Невідповідність розміру заготівки
| Дотримуватися встановлених параметрів
Витримувати розміри заготівки
|
2. Надриви | Недбале витягання деталі з форми
| Дотримуватися правила витягання деталей з форми
| 3. Невідповідність виробу заданим розмірам
| Знос прес-форм. Неправильна збірка частин прес-форм
| Замінити прес-форму. Перевірити форми по інвентарному номеру
| 4. Міхури, губка
| Неправильне розміщення заготівки у формі. Швидке підпресування. Попадання повітря в прес-форму. Великий вміст вологи в заготівці
| Дотримувати правила і режим підпресування. Швидко розкривати прес-форму після витягання її з пресу. Просушити вологу заготівку перед закладкою в прес-форму
| 5. Вм'ятини
| Довільне скорочення режиму вулканізації
| Суворо дотримуватися режиму вулканізації і підпресування
| 6. Пористість
| Вміст в гумі летючих речовин
| Дотримуватися режиму підпресування деталі перед вулканізацією
| 7. Недовулкані-зація
| Зміна температури плит пресу
| Змінити час вулканізації по вказівці майстра
| 8. Шорстка поверхня
| Висока температура плит пресу
| Відрегулювати температуру плит преса
|
Виробництво рукавів дорновим способом
Таблиця 7 - Види дефектів, причини виникнення і заходи по їх знешкодженню
Види дефектів
| Причини виникнення
| Заходи знешкодження
|
1. Включення в зовнішньому і внутрішньому гумовому шарі | Наявність сторонніх частинок
Наявність частинок підвулканізованої гуми
| Застосовувати просіяні інгредієнти
Дотримувати режим змішання інгредієнтів
| 2. Міхури в зовнішньому і внутрішньому гумовому шарі
| Завищення вмісту вологи в компонентах гумової суміші
Порушення технологіч-ного режиму вулканізації
| Застосовувати інгредієнти без завищеного вмісту вологи
Дотримувати режим вулканізації
| 3. Здир внутрішнього гумового шару
| Пошкодження вулкані-зованого внутрішнього гумового шару дорнами
Складка гумової камери при надяганні наконечників
| Застосовувати якісно обчищені дорни
Застосовувати якісні наконечники
| 4. Здир зовнішнього гумового шару
| Неякісне покриття рукавів антиадгезійним складом
| Забезпечити якісне покриття рукавів антиадгезійним складом
| 5. Відшаровування гумового шару від текстильного каркаса
| Незадовільна якість просочувального складу
Незадовільна якість просочених ниток
Осмоленння текстильного каркасу в процесі сушки оплетених рукавів
| Застосовувати якісний просочувальний склад
Застосовувати якісно просочені нитки
Дотримувати температуру і час просушування обплетених рукавів
| 6. Піднесення на зовнішньому гумовому шарі
| Короткочасне уповіль-нення швидкості проходження обплетених рукавів через головку шприц-машини
Неправильно відрегульоване оснащення шприц-машини
| Дотримувати швидкість шприцювання обплетених рукавів
Працювати на правильно відрегульованій шприц-машині
|
Виробництво неформових виробів автоклавним способом
Таблиця 8 – Види браку, причини виникнення і заходи по попередженню
Види браку
| Причини виникнення
| Заходи по попередженню
| 1. Включення сторонніх предметів, підвулканізо-ваної гуми
| Забрудненість робочого місця при екструзії і виготовленні гумової суміші. Погане перемішування суміші. Підгоряння суміші в машині. Підвищена вогкість сумішей і інгредієнтів, великий вміст летючих речовин в каучуках і пом'якшувальних засобах
| Тримати в чистоті робоче місце
Ретельно перемішувати суміш. Дотримуватися режиму шприцювання.
| 2. Пори, міхури
| Порушення режиму підвищення тиску пари в автоклаві при вулканізації
| Застосовувати просушені інгредієнти Дотримувати режим вулканізації в автоклаві
| 3. Деформація виробу
| Попадання повітря в гумову суміш при нерівномірному завантаженні шприц-машини
Деформація під дією сили важ-кості або сторонніх предметів
| Рівномірно подавати суміш в завантажу-вальну воронку
| 4. Нерівномір-ність перетину
| Нерівномірна подача гумової суміші в черв’ячну машину
| Правильно укладати вироби на лоток перед вулканізацією. Не допускати попадання сторонніх предметів на виріб. Рівномірно подавати суміш в черв’ячну машину
| 5. Порізи (риски)
| Попадання сторонніх включень в зазор між шайбою і дорном.
Наявність заусенців на дорні або шайбі.
| Не допускати попадання сторонніх предметів між дорном і шайбою, використо-вувати дорн і шайбу з гладкою поверхнею.
| 6. Перекрут виробів
| Неправильне укладання виробу на лоток або в круг.
Набухання суміші вище за норму.
| Правильно укладати вироби на лоток або в коло. Не допускати набухання суміші вище за норму.
| 7. Відхилення розмірів
| Неправильна настройка черв'ячної машини.
| Налагоджувати черв'ячну машину по інструкції.
|
Виробництво неформових виробів на лінії ЛНВС-90
Таблиця 9 – Види браку, причини виникнення, способи усунення
Види браку
| Причини виникнення
| Способи усунення
| 1. Підвулканізація гумової суміші
| Підвищена температура голівки шприц-машини, збільшена подача гумової суміші
| Налагодити температурний режим нагрівання голівки машини і рівномірне її живлення
|
2. Шорсткість поверхні | Знижена температура гумової суміші, що подається
| Розігріти гумову суміш до заданої температури
| 3. Міхури
| Підвищена пластичність гумової суміші
| Пластичність суміші повинна відповідати заданій
| 4. Відхилення розмірів
| Неправильне налагодження шприц-машини
| Правильно налагодити шприц-машину
| 5. Подовжня смугастість
| Наявність заусенців на шайбі, попадання сторонніх включень між дорном і шайбою
| Замінити шайбу, гумову суміш пропустити через стрейнер
| 6. Механічні включення
| Застосування каучуків та інгредієнтів з включен-нями, забрудненість робочого місця
| Не застосовувати каучуки та інгредієнти з включеннями; дотримувати культуру виробництва
| 7. Шаруватість
| Попадання пилу, змащувального мастила, тальку в суміш
| Не допускати попадання в суміш сторонніх включень
|
Виробництво діелектричних килимків
Таблиця 10 - Види дефектів, причини виникнення, заходи по попередженню
Види дефектів
| Причини виникнення
| Заходу по попередженню
| 1. Передчасна
вулканізація гумової суміші
| Порушення температурного режиму при розігріві або листуванні гумової суміші
| Суворо дотримувати температурний режим при розігріві або листуванні гумової суміші
| 2. Пористість і міхури при листуванні
| Захват гумовою сумішшю повітря при великому зазорі між валками каландра
| Суворо дотримувати задану товщину зазору при листуванні гумової суміші
| 3. Утворення рельєфного візерункового малюнка “ялинка”
| Недостатній розігрів гумової суміші на вальцях. Порушення температурного режиму при каландру-ванні
| Суворо дотримувати тривалості розігріву.
Суворо дотримувати температурний режим при каландруванні
| 4. Нерівномірна товщина листа
| Нерівномірний розігрів гумової суміші
Нерівномірне живлення каландра
| При розігріві бажано перемішувати гумову суміш, ретельно стежити за живленням каландра.
| 5. Наявність сторонніх включень
| Недбале зберігання гумової суміші
| Тримати в чистоті робоче місце
| 6. Пористість і міхури в килимах
| Недостатній тиск стрічки, на пресуючому вулканізуємому виробі
| Суворо дотримувати тиск в притискній стрічці
| 7. Недовулканізовані вироби
| Зниження температури у вулканізаційному барабані
| Суворо дотримувати тиск у вулканізаційному барабані
|
|